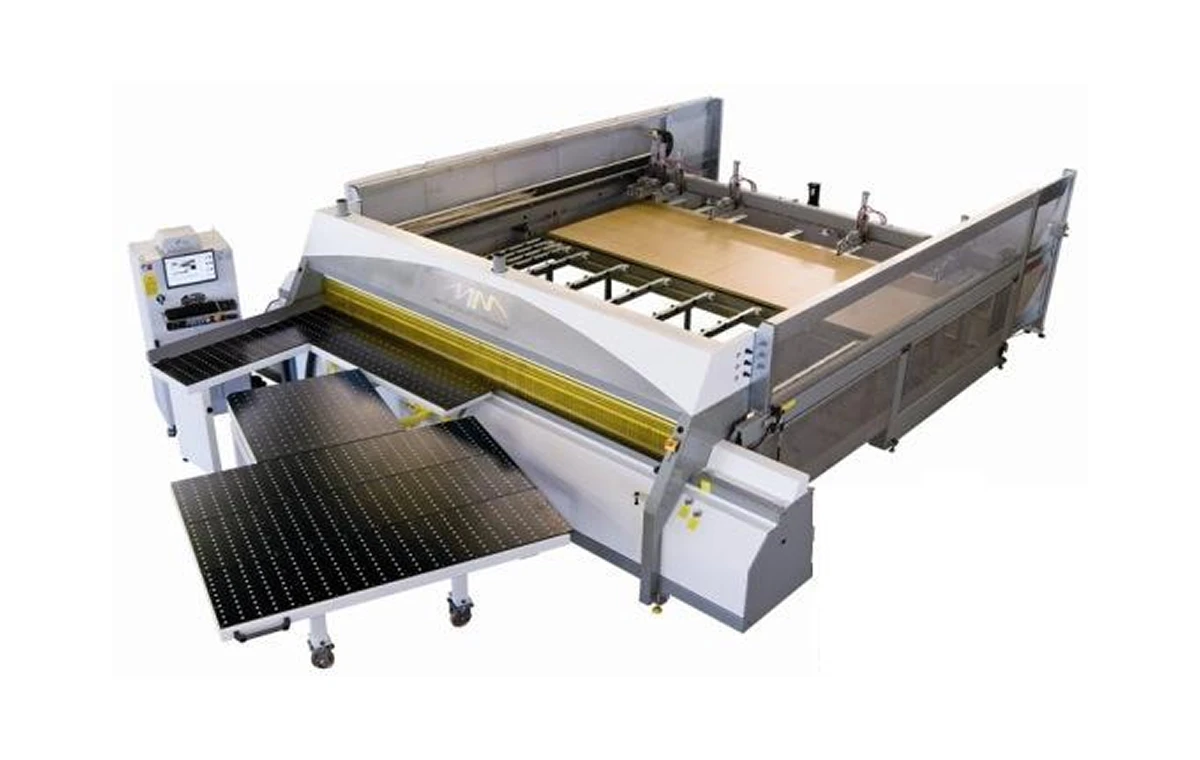
Rotating air flotation table
The patent, which integrates seamlessly with the Piero warehouse, solves the problem of complex frontal movement in single-blade panel saws, especially when dealing with complex cutting patterns. This device is particularly useful for advanced 5-level cutting optimizations, reducing waste and maximizing efficiency with less labor.
Description
CHECK THE STRESS OF HANDLING PANELS ON A ROTATING TABLE
The front rotating table consists of a manually operated table, designed to allow the rotation of one or more panels to be sectioned. It is composed of: a rotating frame on which lies a support surface equipped with an “air flotation table”; the movement occurs by acting on the appropriate handle and, subsequently, by placing the panels, always manually, next to a reference lateral stop
With reference to the reference tables SNOOK CIRIELLO:
- Let’s assume a travel distance of 2 meters
- Let’s consider the movement frequency as 1 move every 5 min. (overestimated frequency)
- The height of the working table is 90-95 cm.
For the above reasons, the above tables provide a maximum recommended effort for a healthy adult male individual of:
28 KG in push and 27 Kg in pull
The maximum dimensions of the workable panel are = AxB = 4,25 mt x 2.2 mt
The maximum cutting height (overlapping more panels) is = H=108 mm
The average density of chipboard panels is:D= 650 kg/m^3
For the above, the maximum capacity of the machine (and therefore the maximum weight to be moved) is:
P = length of the panel pack x width of the pack x height x density = AxBxHxD = 656 Kg.
Obviously, this weight must NOT be lifted by the operator, but simply pushed/rotated by placing the panels in the desired position.
Let’s now evaluate the force required for the translation/rotation of the panel pack. (ref. fig.)
Let’s divide the manual handling action into 2 phases:
1) main rotation for the panel pack
2) small rotation/placement of the panels at the reference stop.
1) The main rotation of the package is on wheels, therefore the rolling friction coefficient will be in the order of 0.015-0.03. (let’s assume an average of 0.02) Also considering an extra weight of the structure of 300kg.
The force to be overcome by the operator is.
(weight of panels + weight of structure)*coeff. Rolling friction = (656+300)*0.02= 19 kg
Within the admissible stress limit.
Il momento resistente d’attrito da vincere vale pertanto : M=2*f*B*r= 45.2 Kg*mt
2) To evaluate the rotation/approach stress, we assume that 2 equal forces of:
656/2= 328 kg. (f) act with an arm B=106 cm (1/4 of a panel).
For symmetry, the rotation axis coincides with the centre of the package.
The panel support surfaces are equipped with a special “air flotation table” to prevent friction; therefore, the friction coefficient “r” between the panels and the support tables varies between 0.03 and 0.1. (we therefore assume on average r= 0.065)
The frictional resistance moment to be overcome is therefore: M=2*f*B*r= 45.2 Kg*mt
Since the movement speeds are so low that any inertial action can be neglected, the rotation torque that the operator must apply coincides only with the frictional resistance moment.
Furthermore, the operator (moving the panels from the corner) uses a lever arm L, therefore the force he must apply (Foperator) is:
Foperatore*L= 45.2 Kg*m from which
Foperatore= 18,9 Kg.
However, this value is still lower than those of SNOOK CIRIELLO and therefore acceptable
The above, as already stated, applies in the hypothesis of rotation of panels of the maximum workable dimensions stacked for the maximum sectionable height.
However, during the working day, the operator will perform a greater number of rotations than the “sub-formats” of the master panel; that is, typically “strips” of about 700 mm. wide.
In this case, repeating the above calculations results in a rotation stress by the operator of only 6-8 kg.
This excellent result is obtained thanks to the wide continuous support guaranteed to the panels by the rotating table, combined with the air flotation table.
The patent that integrates perfectly with the “Piero” system, solves the problem of complex frontal movement in single-blade panel saws, especially when dealing with complex cutting patterns. This device is particularly useful for advanced optimizations at 5 cutting levels, reducing waste and maximizing efficiency with less manpower.
The main improvements introduced by the combination with the Rotating Air Flotation Table on the Top Saw panel saw include:
- The system allows you to easily rotate not only pre-cuts or head cuts, but also packs of longitudinal strips for cross cuts, without operator effort and without the need for rails or guides.
- It allows you to make complex cuts to optimize panel waste with a single operator, improving productivity and reducing labour costs.
- It is more economical than a rear-loading platform.
- Compared to automatic rotating systems, our system is faster and safer, avoiding damage to panels, even thin or delicate ones.
- The divisible tables allow loading and unloading directly from the front of the machine, with ease of operation with a forklift or forklift.
- The system allows a continuous flow of work, without stopping the cutting cycle, and facilitates the unloading of large packages or strips.
- When the table is rotated, it is possible to load and unload from both sides of the machine, optimizing space.
- For small panels, the operator can work directly in the cutting area, while for large panels, the operator moves laterally.
- The table can be easily integrated with automatic systems for loading and unloading panels.
- The mechanical device is simple, robust, requires no maintenance or adjustments, and includes safety photocells to prevent incorrect use.
Video
Quality
High quality mechanical components, long life and reliability.
Efficiency
Compact and high-performance. Quick setup and simplified production processes. Greater automation and flexibility in the costing of the final product.
Easy to use
Intuitive, fast and efficient software. Work lists for easy production start-up.
Environment
Suction system for a clean and comfortable environment.